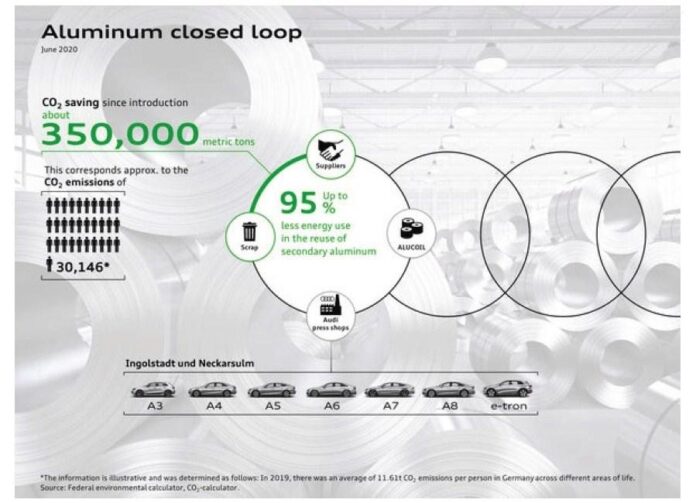
La marca de los cuatro anillos procesa el material para su reutilización a través de un ciclo cerrado de reciclaje en sus plantas de Neckarsulm e Ingolstadt.
La producción del aluminio que es empleado en la fabricación de vehículos implica un alto consumo energético. Es por eso que Audi procesa el material sobrante para su reutilización mediante un ciclo cerrado de reciclaje.
De esta forma, la marca de los cuatro anillos consigue ahorrar valiosas materias primas y a su vez contribuye a que los automóviles inicien su fase de uso desde un mejor equilibrio ambiental. Según la compañía, consiguió ahorrar más de 350.000 toneladas de emisiones de CO2.
Más información, en el comunicado de prensa a continuación…
COMUNICADO DE PRENSA – AUDI ARGENTINA
Audi ahorró más de 350.000 toneladas de emisiones de CO2 desde la implementación del circuito cerrado de aluminio
La marca de los cuatro anillos tiene una larga tradición en la utilización del aluminio para la fabricación. En 1994 presentó el primer Audi A8 con tecnología de construcción ligera Audi Space Frame, lo que significó un logro pionero en la industria automotriz. En la actualidad continúa utilizando el aluminio junto a otros materiales ligeros como parte de una tecnología de construcción ligera multi-material. Dado que para producir aluminio se requiere mucha energía, Audi procesa el material para su reutilización mediante un ciclo cerrado de reciclaje. Esto permite ahorrar valiosas materias primas y contribuye a que los vehículos inicien su fase de uso desde un mejor equilibrio ambiental. Las naves de prensa de las plantas de Ingolstadt y Neckarsulm utilizan aluminio reciclado para fabricar piezas en las líneas de producción de los modelos Audi A3, A4, A5, A6, A7 y A8, así como para componentes de los Audi e-tron. Otras fábricas de la marca también adoptarán este procedimiento en un futuro cercano.
“El uso eficiente de los recursos es tan importante para nosotros como la reducción de las emisiones de CO2”, declara Marco Philippi, Director de Estrategia de Compras de Audi AG. “La energía necesaria para la reutilización de aluminio secundario es hasta un 95% inferior que la que se necesita en el caso del aluminio primario”, asegura.
Audi introdujo el circuito cerrado de aluminio en sus instalaciones de Neckarsulm en 2017. En este proceso, la chapa de aluminio sobrante generada en la nave de prensado se devuelve directamente al proveedor, que lo prepara y reprocesa para obtener aluminio secundario reciclado de igual calidad, que posteriormente Audi utiliza en la línea de producción.
La marca de los cuatro anillos lleva a cabo este proceso con dos proveedores, lo que le permite incrementar la cantidad de aluminio que entra en el ciclo cerrado. Gracias a ello, Audi logró ahorrar aproximadamente 150.000 toneladas de emisiones de CO2 en 2019, dos tercios más que en el año anterior.
La fábrica de Ingolstadt también ha introducido recientemente el circuito cerrado de aluminio, y la de Györ planea hacerlo el año próximo. Otras instalaciones y líneas de producción de Audi lo implementarán también en el futuro.
El aluminio secundario se utiliza actualmente en varias partes de la carrocería de los Audi A3, A4, A5, A6, A7 y A8, y también en distintos componentes de los Audi e-tron.
La transición hacia la movilidad eléctrica aumenta la proporción de emisiones de CO2 que son directamente atribuibles a la cadena de suministro. Tanto en la propia cadena como en los procesos de producción previos, Audi generará casi una cuarta parte de las emisiones de CO2 para 2025, en base al promedio previsto de la flota.
La marca de los cuatro anillos está trabajando con sus proveedores para implementar medidas que tengan un impacto en esta fase inicial de la producción. La compañía comenzó a desarrollar en 2018 un programa de acción junto con sus proveedores para encontrar medidas que contribuyeran a la reducción de emisiones de CO2 en la cadena de suministro. Se han identificado oportunidades para hacerlo con nuevos circuitos cerrados de materiales, con el aumento de utilización de materiales secundarios o procesados y a través del uso de electricidad verde. Se espera que estas medidas sean plenamente efectivas en 2025 y que permitan realizar un ahorro potencial de CO2 de 1,2 toneladas por vehículo en promedio.